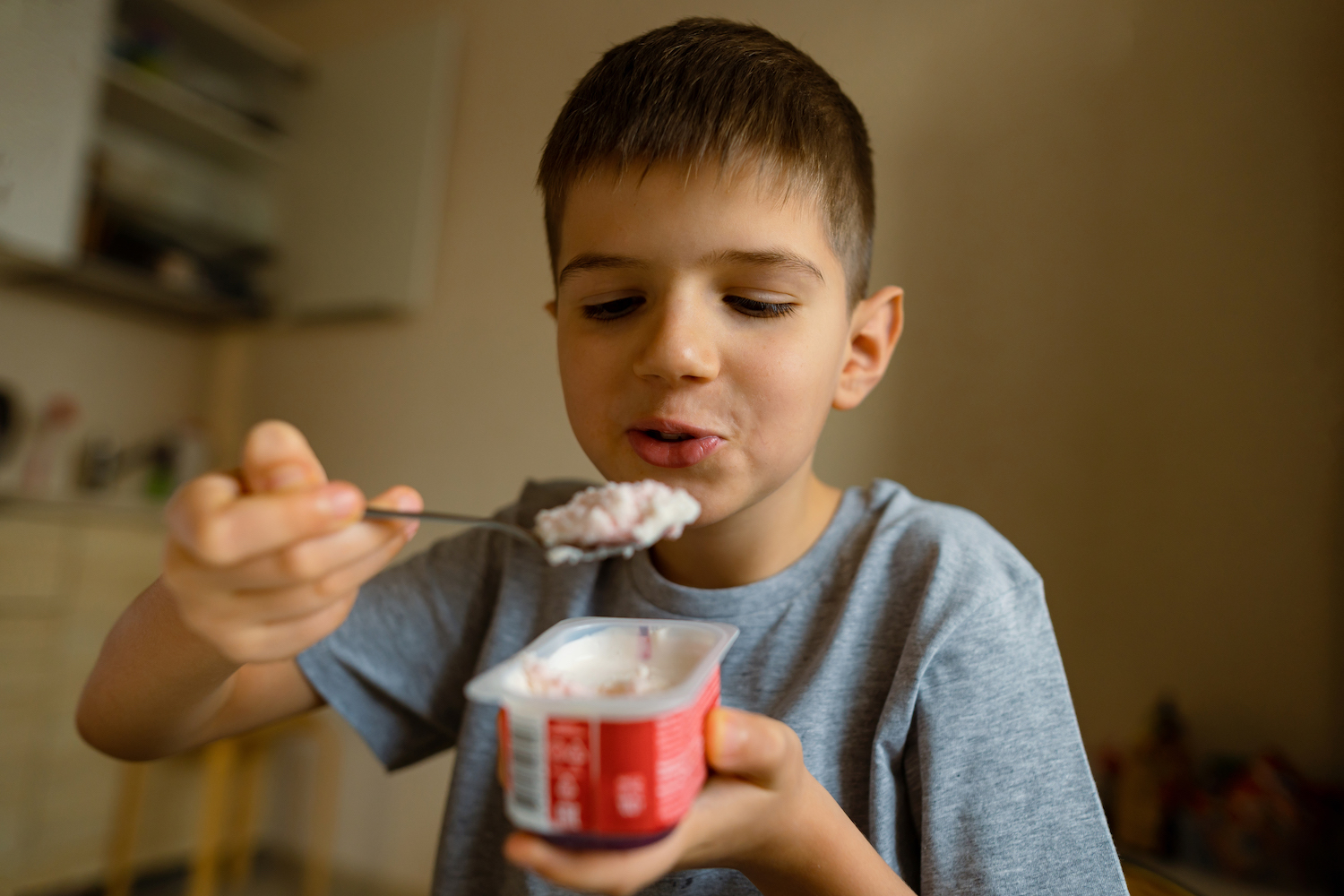
Leak detection and package integrity testing for food safety: What types of products should be tested?
Package integrity testing can be done on a wide range of products that require special attention in the integrity testing phase before they are sold. This is necessary because of the characteristics of the product or of the consumers who will consume them. They include:
- Cans: cans are commonly used in the food industry and testing is done on all foods stored in metal containers (two-piece can), such as tuna, vegetables, tomato sauce and so on.
- Oil cans or other metal containers (three-piece can)
- Aerosol cans (both empty and filled)
- Energy drinks and other beverages
- Baby food and products for children
- Coffee pods
- Ready meals, food trays
- Pet food
- Milk and dairy products
Basically, all products contained in rigid containers such as cans can be tested. So can foods sold in containers closed with a heat-sealed lid, like many ready-to-eat pre-cooked products or other common foods such as yoghurt, milk, baby foods and so on.
Test types and methods used
When testing food product packaging, we check that the container has no cracks, holes or micro-holes that would prevent it from effectively performing its function as a barrier to the external environment.
We can use different types of tests to do this, depending on the type of packaging and the level of performance required on the production line. Remember that the pace of production is generally very rapid in the food industry, so tests that do not slow down production speed are needed, as plant efficiency would be compromised. The most efficient methods in this regard are:
- Vacuum Decay Method (VDM): this technology uses a vacuum to detect leaks in a sealed container without destroying or damaging the product in any way. Once a product has been tested and found to comply with standards, it can be re-introduced on the line and ultimately be sold. The product is inserted in a test chamber, inside which a vacuum is created. Pressure variation after a given time interval is analysed to identify the presence and extent of leaks.
To reduce the time required for testing, we can insert only the part of the container at greatest risk in the test chamber. For food stored in bottles, for example, only the cap would be tested. This means that we can use smaller test chambers, so a vacuum can be created more quickly and pressure values detected more rapidly.
- Lid deflection: this testing method is especially suitable for testing containers with plastic or aluminium films that are heat sealed to the container. In this case, special sensors or optical laser detectors check the proper positioning of the protective membrane. This type of test is particularly useful in the food sector, because the container’s integrity can be checked without the product actually being touched, providing excellent guarantees in terms of limiting contamination.
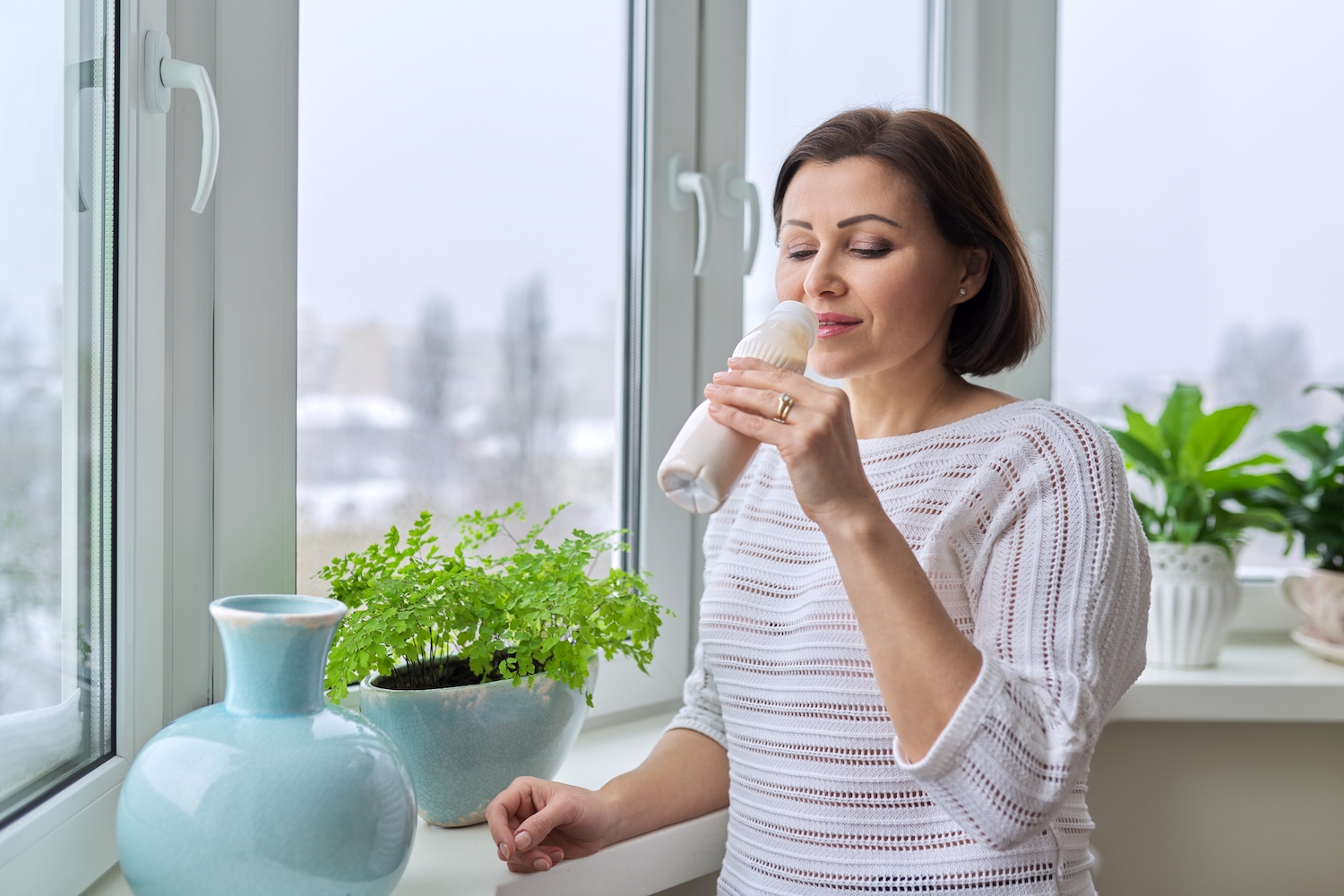
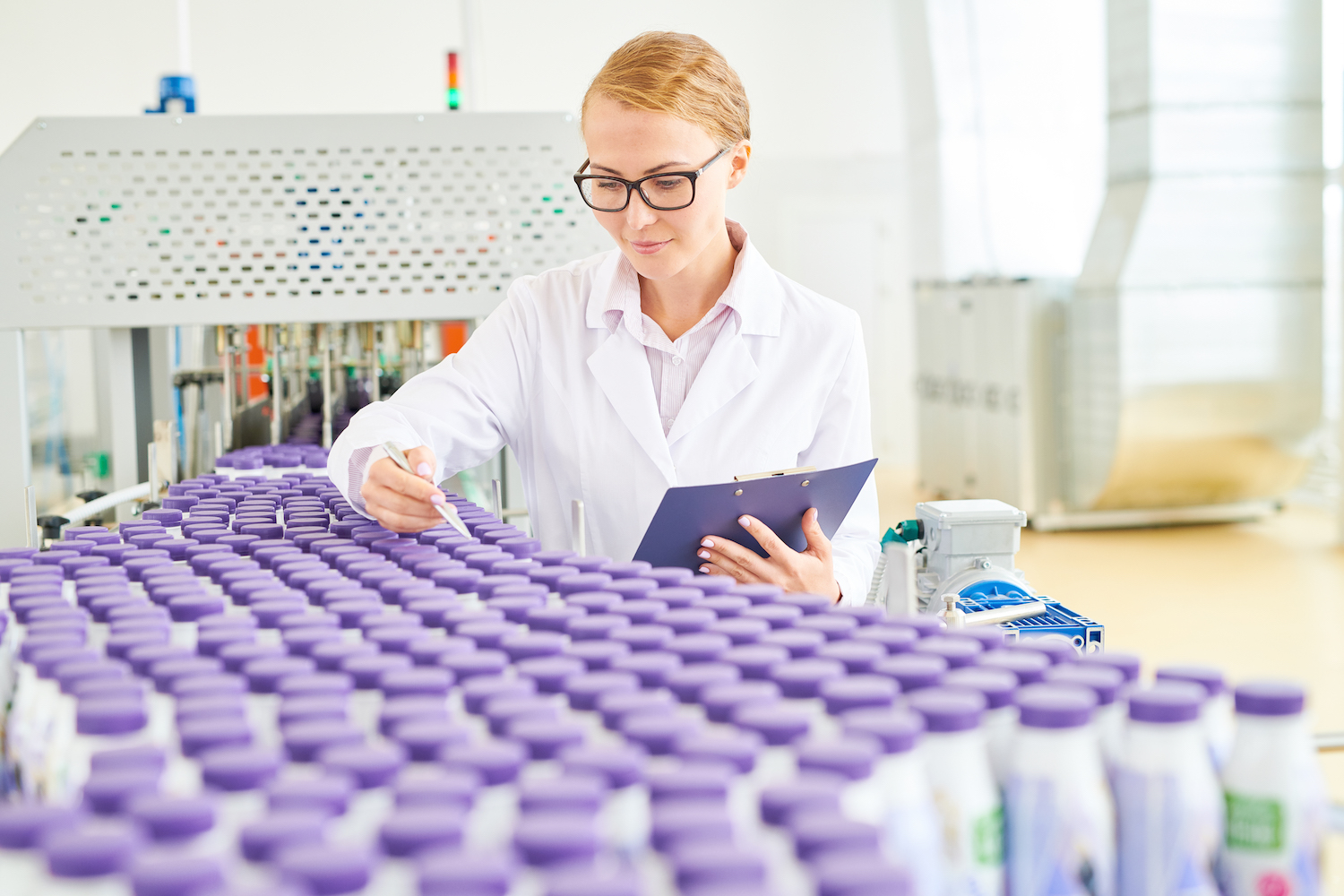
The challenges of food testing
Testing food products poses a number of challenges. The unique nature of food products requires that the tests be performed with particular care, but not to the detriment of efficiency in the production plants as a whole. Some of the main challenges of food testing are:
1. Speed
Whatever the test method chosen, the machines used must be capable of operating even at high or very high speeds. These machines are installed on lines that work at high speeds (up to 1,200 pieces/minute), and package integrity testing cannot slow down normal production flow. This means that we need to design systems capable of supporting such speeds.
2. Accuracy
Given the unique nature of the products tested, testing machines for the food industry must guarantee high levels of quality, accurately identifying all damaged products, without producing false rejects. For this to be possible, the components performing testing must be carefully designed to maximise their sensitivity.
3. Speed in managing format changes
Food manufacturers offer a wide range of products packaged in containers that are often made of the same material but in different sizes (e.g., companies that produce canned tuna almost always offer identical products in terms of content and shape, but of different sizes). This is why testing machines have to be able to manage product format changes correctly without slowing down production.
4. Delicate handling
Some food products have to be handled with special care (e.g., foods in decorated or screen-printed containers) to prevent damage like marks, scratches or dents. So, during machine design, proper attention has to be paid to product handling, to ensure that the mechanical arms moving the containers are made of special materials that won’t damage, crush or scratch the containers in any way when inserting them into the test chamber.
5. Product characteristics
The characteristics of food products affect the type of test that needs to be done and the method that should be used. For example, milk testing needs to take into account the fact that the product must be bottled in an aseptic environment, since it can be contaminated by micro-organisms if it comes into contact with oxygen. We need to include these types of considerations when designing the plant, so that we provide industries with tools that truly meet their needs.
Why package integrity testing is so important
Finally, remember that, unlike pharmaceutical products, GMP for the food & beverage sector do not require companies to implement package integrity control systems for leak detection.
This means that using such tests is absolutely voluntary, and depends on each manufacturer’s internal policies. However, we must emphasise that these tests offer extremely positive effects in terms of both product quality, and efficiency and productivity.
Package integrity testing not only guarantees that every product sold is sealed perfectly and complies with standards, but can also identify possible malfunctions on the production line early on, so that they can be corrected before their consequences become too significant. For example, if the number of non-compliant products increases for no apparent reason, or if a certain type of unexpected defect is encountered frequently, the manufacturer can investigate the cause of the problem in a timely manner, preventing the situation from worsening and improving plant performance. This can avoid product recalls, which are extremely harmful from an economic point of view and can damage customer loyalty.